97% SiC Black Silicon Carbide as The Refractory
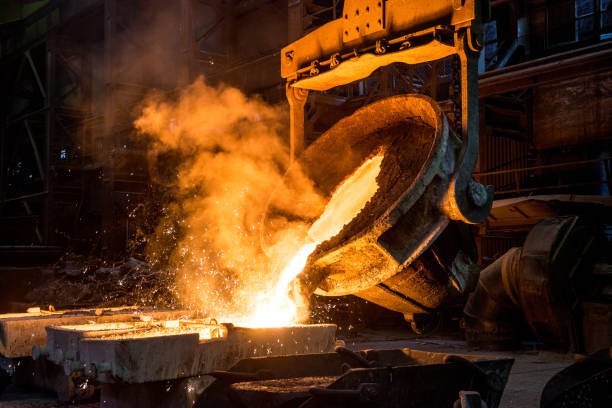
كربيد السيليكون, more specifically, black silicon carbide (كذا), is a powerful and versatile material offering numerous benefits for refractory use. Thanks to its high-temperature tolerance and wear resistance, 97% SiC black silicon carbide has become the go-to solution for various industrial processes.
Understanding Silicon Carbide (كذا)
To understand the impact of 97% SiC black silicon carbide in the refractory industry, we must first understand what silicon carbide is. Silicon carbide is an incredibly hard, synthetically produced crystalline compound of silicon and carbon. Recognized for its resistance to high temperatures, thermal shock, and mechanical stress, silicon carbide is a versatile material used across many industries.
- High Hardness and Strength: Silicon carbide boasts a hardness of 9 على مقياس MOHS, surpassed only by diamond, cubic boron nitride, and boron carbide.
- Excellent Thermal Conductivity: SiC is known for its superb heat dissipation, making it an ideal material for applications requiring high thermal conductivity.
- Chemical Inertness: SiC exhibits excellent resistance to strong acids, alkalis, and other harsh chemicals, maintaining its properties even under extreme conditions.
The Composition: 97% SiC Black Silicon Carbide
97% SiC black silicon carbide refers to the purity of the silicon carbide. In this case, 97% of the material is made up of silicon carbide, offering superior properties compared to lower purity counterparts. This purity level ensures optimal performance, متانة, and longevity, making it an ideal choice for refractory applications.
Manufacturing Process of 97% SiC Black Silicon Carbide
Producing high-quality, 97% SiC black silicon carbide is a complex process involving several stages.
- Material Mixing: The process begins with the mixing of raw materials, primarily quartz sand (SiO2), petroleum coke (C), and high-quality carbon (C).
- High-Temperature Fusion: The mixed materials are then heated to temperatures above 2000°C in an electric resistance furnace. This extreme heat triggers a reaction that forms basic SiC.
- Cooling and Grinding: After the fusion process, the material is cooled, crushed, and ground into granules or powder form, creating the base product of black silicon carbide.
Why Choose 97% SiC Black Silicon Carbide in Refractory Applications
When it comes to refractory applications, 97% SiC black silicon carbide has several standout attributes that make it an excellent choice:
- High-Temperature Resistance: Its ability to withstand extreme temperatures makes it ideal for use in furnaces and kilns.
- Oxidation Resistance: The high SiC content in 97% black silicon carbide also grants it superior resistance to oxidation at high temperatures.
- Abrasion and Wear Resistance: Its impressive hardness ensures excellent wear resistance, reducing the need for frequent replacements and improving overall operational efficiency.
- Chemical Stability: Its ability to resist interaction with a variety of chemicals prevents material degradation, ensuring the long-term performance of the refractory components.
خاتمة
The introduction of 97% SiC black silicon carbide into the refractory industry has revolutionized many traditional practices. With its impressive list of properties including high-temperature tolerance, wear resistance, and chemical stability, this versatile material continues to prove its value in a myriad of industrial applications. By understanding its properties, manufacturing process, and the benefits it provides, industries can effectively leverage 97% SiC black silicon carbide for improved efficiency and reliability in their refractory applications.
قد تكون مهتم ايضا ب…
اتصل بنا
احصل على عرض أسعار مجاني
أسس في 2001, HSA هي الشركة الرائدة في مجال توفير أبخرة السيليكا والمواد الكاشطة في الصين, وأيضًا المصدر المتميز للمنتجات عالية الأداء للصناعات الخرسانية والمواد الكاشطة.