Black Fused Alumina
Black fused alumina is a highly durable and versatile abrasive material that has a wide range of applications in various industries. Its unique combination of physical and chemical properties makes it suitable for abrasive blasting, surface preparation, polishing, refractory materials, and anti-skid flooring applications. Its high durability, low dust generation, versatility, and cost-effectiveness make it an ideal choice for industrial processes.
Request Custom Quote
Particle Size
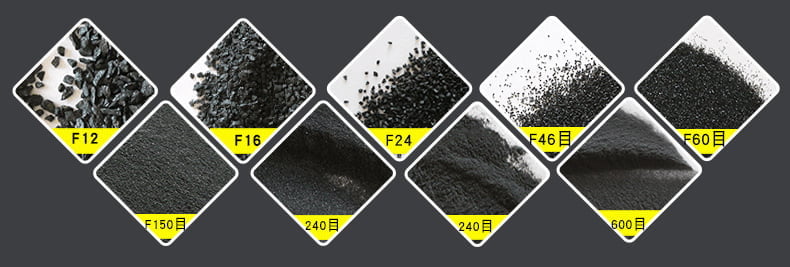
- Common particle size of refractory materials: 0-1, 1-3, 3-5, 5-8mm, 100, 200, 325 mesh
- Common particle size of abrasives: 12, 14, 16, 24, 30, 36, 46, 60, 80, 100, 120, 150, 180, 200, 220, 240, 280, 325 mesh.
- Common micropowder for polishing and grinding: 400, 600, 800, 1000, 1500, 2000, 3000 mesh
- The granularity of the product can be processed according to the granularity required by the user.
Features
- Crystal Structure
Black fused alumina has a hexagonal crystal structure and is composed of aluminum, iron, and oxygen. The iron content gives the material its black color. - Hardness and Toughness
Black fused alumina has a high hardness rating of 9 on the Mohs scale, making it a suitable material for grinding and polishing hard surfaces. At the same time, the material exhibits excellent toughness, which allows it to withstand high impact and pressure without breaking. - Melting Point
Black fused alumina has a high melting point of around 2,050°C, making it a heat-resistant material suitable for high-temperature applications.
Applications
- Abrasive Blasting
Black fused alumina is a popular abrasive material used in abrasive blasting. Its high hardness and toughness make it effective in removing rust, paint, and other surface coatings from metal surfaces. It is also used for surface preparation prior to painting or coating, as it creates a roughened surface that promotes adhesion. - Surface Preparation
In addition to abrasive blasting, black fused alumina is also used for surface preparation in various industries. It is used to roughen and clean surfaces of different materials, including metals, ceramics, and composites. Surface preparation with black fused alumina improves the adhesion and bonding of subsequent coatings, such as paints and sealants. - Polishing and Lapping
Black fused alumina is also used as an abrasive material for polishing and lapping applications. Its high hardness and uniform particle size make it effective in achieving a smooth and uniform surface finish on metals, glass, and ceramics. It is commonly used in the production of optical lenses, electronic components, and precision parts. - Refractory Materials
Black fused alumina is a refractory material with excellent high-temperature stability and chemical resistance. It is used in the production of refractory materials such as bricks, castables, and monolithic refractories. These materials are used in the construction of furnaces, kilns, and other high-temperature applications. - Anti-Skid Flooring
Black fused alumina is also used in the production of anti-skid flooring materials. Its high hardness and durability make it an ideal material for creating slip-resistant surfaces in various applications, including industrial flooring, stairs, and walkways.
Parameters
Item | Indicators |
Color | Black |
Crystal | Trigonal system |
Hardness(mohs) | >=9.0 |
Melting Point(℃) | 2050 |
The Maximum Temperature | 1850 |
True Density(g/cm3) | >=3.50 |
Linear expansion coefficient(0-1600℃) | 7-9 |
FAQ
Contact Us
Get Free Quotation
Founded in 2001, HSA is a leading provider of Silica Fume and Abrasives in China, and also the premium source of high-performance Products for concrete and abrasives industries.