Exploring the Versatility of Silicon Carbide Coatings
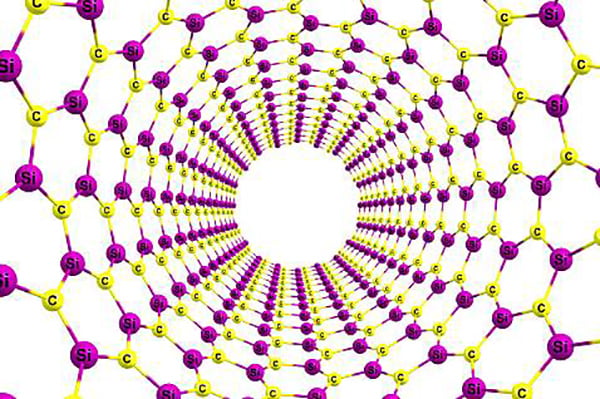
In the realm of advanced materials, silicon carbide (SiC) has emerged as a true powerhouse, offering a unique combination of exceptional properties that have revolutionized various industries. From its outstanding hardness and thermal stability to its chemical inertness and high wear resistance, SiC coatings have proven their mettle in a wide range of applications, making them an indispensable choice for numerous sectors.
The Remarkable Properties of Silicon Carbide
Silicon carbide is a compound composed of silicon and carbon, forming a highly stable and durable crystalline structure. Its exceptional properties stem from the strong covalent bonds between its constituent elements, resulting in a material with unparalleled characteristics.
- Hardness and Wear Resistance: One of the most notable features of SiC is its remarkable hardness, surpassed only by diamond. This hardness translates into exceptional wear resistance, making SiC coatings ideal for applications where durability and longevity are paramount. From cutting tools and bearings to components subjected to abrasive environments, SiC coatings offer unmatched protection against wear and tear.
- Thermal Stability: Silicon carbide boasts an impressive thermal stability, maintaining its structural integrity and properties at temperatures exceeding 1600°C (2912°F). This characteristic makes SiC coatings invaluable for applications involving high-temperature environments, such as in the aerospace, automotive, and power generation industries.
- Chemical Inertness: Another significant advantage of SiC coatings is their high resistance to chemical attack. They are largely impervious to most acids, alkalis, and organic solvents, making them well-suited for use in harsh chemical environments encountered in the chemical processing, petrochemical, and pharmaceutical sectors.
- Oxidation Resistance: Silicon carbide exhibits excellent resistance to oxidation, even at elevated temperatures. This property ensures that SiC coatings maintain their integrity and performance in oxygen-rich environments, preventing degradation and extending the service life of coated components.
- Electrical and Thermal Conductivity: Depending on its composition and processing conditions, SiC can possess varying degrees of electrical and thermal conductivity. This versatility allows SiC coatings to be tailored for applications ranging from semiconductor devices to thermal management systems.
Applications of Silicon Carbide Coatings
The unique combination of properties offered by SiC coatings has led to their widespread adoption across numerous industries, revolutionizing various sectors and enabling technological advancements.
- Cutting Tools and Wear Parts: SiC coatings are widely used in the manufacturing sector, particularly for cutting tools and wear-resistant components. Their exceptional hardness and wear resistance significantly extend the lifespan of cutting tools, reducing downtime and maintenance costs. Similarly, SiC coatings protect wear parts, such as bearings, gears, and valves, from abrasive environments, ensuring reliable and efficient operation.
- Aerospace and Automotive Industries: The thermal stability and oxidation resistance of SiC coatings make them ideal for high-temperature applications in the aerospace and automotive sectors. These coatings are used to protect engine components, turbine blades, and exhaust systems from extreme temperatures and harsh operating conditions, improving performance and durability.
- Chemical Processing: The chemical inertness of SiC coatings renders them invaluable in the chemical processing industry. They are employed to protect equipment, such as reactors, pipes, and valves, from corrosive media, ensuring safe and efficient operations while minimizing maintenance requirements.
- Semiconductor and Electronics: The unique electrical and thermal properties of SiC have led to its widespread use in the semiconductor and electronics industries. SiC coatings are employed in the fabrication of high-power electronic devices, power modules, and sensors, enabling improved energy efficiency and higher operating temperatures.
- Biomedical Applications: The biocompatibility and chemical inertness of SiC coatings have opened up opportunities in the biomedical field. These coatings are used to protect implants, prosthetics, and surgical instruments, preventing corrosion and minimizing the risk of adverse reactions in the human body.
Deposition Techniques for Silicon Carbide Coatings
To harness the full potential of SiC coatings, various deposition techniques have been developed and refined over the years. Each method offers unique advantages and is tailored to specific applications and substrate requirements.
- Chemical Vapor Deposition (CVD): CVD is a widely used technique for depositing SiC coatings. In this process, gaseous precursors, such as methyltrichlorosilane and hydrogen, are introduced into a reaction chamber containing the substrate. Through a series of chemical reactions and thermal decomposition, the SiC coating is formed on the substrate surface, offering excellent adhesion and uniformity.
- Physical Vapor Deposition (PVD): PVD techniques, such as sputtering and evaporation, are employed for depositing SiC coatings. These methods involve the physical transfer of SiC material from a target source onto the substrate, resulting in highly dense and adherent coatings. PVD processes are particularly suitable for coating complex geometries and achieving precise thickness control.
- Plasma-Enhanced Chemical Vapor Deposition (PECVD): PECVD combines the principles of CVD with the use of a plasma environment. By introducing a plasma discharge into the reaction chamber, the deposition process is enhanced, allowing for lower deposition temperatures and improved coating properties. PECVD is particularly useful for depositing SiC coatings on temperature-sensitive substrates.
- Hybrid Processes: In some cases, a combination of deposition techniques may be employed to optimize the performance and characteristics of SiC coatings. For instance, PVD methods can be used to deposit an initial adhesion layer, followed by CVD or PECVD to build up the desired SiC coating thickness and properties.
Challenges and Future Developments
While SiC coatings have proven their worth in numerous applications, there are still challenges and opportunities for further development and optimization.
- Cost and Scalability: One of the primary challenges surrounding SiC coatings is their relatively high cost, particularly for large-scale applications. Ongoing research efforts are focused on developing more efficient and cost-effective deposition processes to make SiC coatings more accessible and economically viable for a broader range of industries.
- Substrate Compatibility: The successful deposition of SiC coatings relies on the compatibility between the coating and the substrate material. Efforts are underway to expand the range of compatible substrates, enabling the application of SiC coatings on a wider variety of materials, including polymers and composites.
- Nanostructured SiC Coatings: Advancements in nanotechnology have opened up exciting possibilities for SiC coatings. Nanostructured SiC coatings, with their unique properties and enhanced surface area, hold promise for applications in catalysis, energy storage, and biomedical devices, among others.
- Multifunctional Coatings: Research is also focused on developing multifunctional SiC coatings that combine multiple desirable properties. For instance, incorporating elements or compounds into the SiC matrix can impart additional functionalities, such as self-lubricating, antibacterial, or sensing capabilities.
As the demand for advanced materials continues to grow, the versatility and exceptional properties of silicon carbide coatings position them as a key enabler for technological advancements across diverse sectors. Through continued research and development, these coatings will undoubtedly play a pivotal role in pushing the boundaries of material performance and enabling innovative solutions to the challenges of the future.
You might also be interested in…
Contact Us
Get Free Quotation
Founded in 2001, HSA is a leading provider of Silica Fume and Abrasives in China, and also the premium source of high-performance Products for concrete and abrasives industries.