Unveiling the Power of Silicon Carbide Cutting Tools
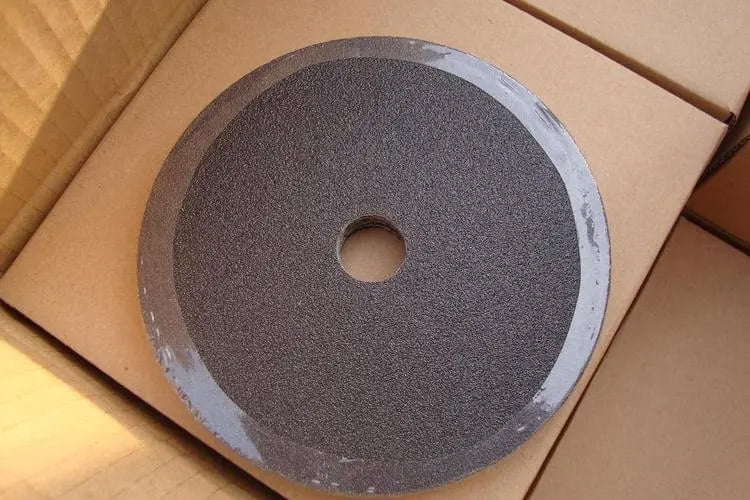
In the realm of advanced materials, silicon carbide (SiC) stands as a remarkable compound. Known for its exceptional properties, SiC is widely used in various industries, particularly in the creation of cutting tools. These tools have revolutionized the way we approach precision machining and material shaping.
What is Silicon Carbide?
Silicon carbide, a compound of silicon and carbon with a chemical formula SiC, exhibits a remarkable combination of properties that make it a preferred choice in cutting tool fabrication. It boasts extreme hardness, excellent wear resistance, and remarkable thermal stability. Its crystalline structure is akin to that of diamond, contributing to its superior performance in high-stress environments.
Why is it Used in Cutting Tools?
Silicon carbide’s attributes are harnessed effectively in cutting tool applications due to its incredible hardness. Cutting tools, tasked with efficiently removing material from workpieces, need to maintain their sharpness and integrity during the machining process. Silicon carbide’s hardness ensures that the cutting edges remain intact even when subjected to intense heat and mechanical stress. This characteristic directly translates to longer tool life and improved machining precision.
Benefits of Silicon Carbide Cutting Tools
The utilization of silicon carbide in cutting tools presents a plethora of advantages that bolster its prominence in modern machining processes.
1. Hardness: Silicon carbide ranks amongst the hardest materials, making it exceptionally resistant to wear and deformation. This quality ensures that cutting edges retain their sharpness for extended periods, enabling consistent and accurate material removal.
2. Wear Resistance: In industries where tools interact with tough and abrasive materials, wear is a major concern. Silicon carbide cutting tools excel in this aspect, as their wear-resistant nature minimizes the need for frequent tool changes, leading to enhanced productivity and cost savings.
3. High Temperature Resistance: Machining processes generate considerable heat, which can significantly affect tool performance. Silicon carbide’s exceptional thermal stability allows these tools to maintain their strength and cutting performance even at elevated temperatures, contributing to prolonged tool life and consistent machining results.
4. Chemical Inertness: Certain machining applications involve corrosive environments or materials that can react with tools. Silicon carbide’s chemical inertness protects the cutting tools from chemical degradation, expanding their application range and ensuring tool longevity.
Types of Silicon Carbide Cutting Tools
Silicon carbide cutting tools can be classified into several types, each tailored for specific machining tasks.
1. Plain Silicon Carbide Tools: Plain SiC tools are single-crystal structures that exhibit exceptional hardness and wear resistance. These tools are ideal for high-speed machining and precision applications.
2. Coated Silicon Carbide Tools: In this category, SiC tools are coated with thin layers of other materials to enhance their performance further. Coatings can improve heat dissipation, reduce friction, and enhance chip evacuation, all contributing to better tool longevity and improved machining efficiency.
3. PCBN (Polycrystalline Cubic Boron Nitride) Tools: While not pure silicon carbide, PCBN tools combine polycrystalline cubic boron nitride with SiC grains. These tools offer exceptional hardness, heat resistance, and superior performance in high-speed machining of hardened steels and other hard materials.
Applications of Silicon Carbide Cutting Tools
The versatility of silicon carbide cutting tools lends itself to a wide array of applications across diverse industries.
1. Metalworking: SiC cutting tools excel in metalworking applications, including turning, milling, and drilling. Their high temperature resistance and wear properties enable precise shaping and machining of various metals and alloys.
2. Woodworking: In woodworking, SiC tools provide the durability and precision required to cut and shape wood with accuracy. Their resistance to wear and heat ensures prolonged sharpness, leading to consistent results in carving and crafting.
3. Plastics Machining: Plastics machining demands tools that can handle both the softness of plastics and the potential heat generated during machining. Silicon carbide cutting tools offer the balance of sharpness and heat resistance necessary for efficient plastics machining.
4. Composites Machining: Modern composites, often comprised of tough materials like carbon fibers embedded in a matrix, require tools that can handle both the fibers’ abrasiveness and the matrix’s toughness. SiC cutting tools provide the durability and precision needed for effective composites machining.
5. Stonework: SiC tools are also employed in stonework applications, where their hardness and wear resistance are put to the test in shaping and sculpting stone materials.
Advantages and Disadvantages
While silicon carbide cutting tools offer numerous benefits, they are not without limitations.
Advantages:
1. Hardness: The exceptional hardness of silicon carbide cutting tools ensures prolonged sharpness and precise machining.
2. Wear Resistance: Their wear resistance reduces the frequency of tool changes, boosting productivity and reducing downtime.
3. High Temperature Resistance: SiC tools maintain their cutting performance even at high temperatures, enhancing tool longevity.
4. Chemical Inertness: The chemical inertness of silicon carbide protects tools from degradation in corrosive environments.
Disadvantages:
1. Brittleness: Silicon carbide tools are brittle, making them susceptible to chipping or breaking under certain machining conditions.
2. High Cost: The advanced manufacturing processes and materials used in SiC cutting tools contribute to their relatively higher cost compared to conventional tools.
Conclusion
In the realm of cutting tools, silicon carbide has emerged as a transformative material, offering unparalleled advantages in precision machining and material shaping. Its exceptional hardness, wear resistance, high-temperature stability, and chemical inertness make it an invaluable asset across various industries. However, its brittleness and higher cost warrant careful consideration. When selecting cutting tools, understanding the specific application, material, and machining conditions is crucial. Silicon carbide cutting tools shine brightest when tasked with challenging materials and demanding machining environments, where their unique properties can be fully harnessed to achieve remarkable results.
You might also be interested in…
Contact Us
Get Free Quotation
Founded in 2001, HSA is a leading provider of Silica Fume and Abrasives in China, and also the premium source of high-performance Products for concrete and abrasives industries.